We are often asked if we use Resin injection (also known as Polyurethane injection) for Structural Foundation issues such as subsidence or movement within one’s homes, and in our opinion, it is a hard ‘no’ from us.
We’d like to offer our findings to explain why we came to that conclusion so consumers can make an informed decision for themselves when dealing with the visual signs such as cracks in exterior walls, cracks in gyprock in walls, and other areas that may require foundation investigation in a residential property. This document is intended to empower consumers to have all the facts at hand so you can make an informed decision about the best way forward for you, your home and your family.
Section 1
The lay of the land – the foundation repair industry:
In the vast Australian landscape, the soil beneath our homes is constantly shifting and changing, which can cause building foundations to fail if not maintained and or addressed correctly.
The reactivity of the soils beneath a property will play a part in how our homes behave over the life of the structure, including influences that typically contribute to the way the clays interact with the home over its life such as: fill settling differentially across the site, inadequate and poorly maintained site drainage, landscaping, weather events, such as El Nina, El Nino etc.
This in turn plays an important role in the extent of the damage observed and the method of underpinning best suited to support the conditions of the home and the site to arrest the damage either through stabilisation and or hydraulic lifting of your home. Soils are identified by Site Classification in accordance with ‘Australian Standards AS 2870/2011, Residential Slabs & Footings’.
Further, the National Construction Code of Australia (NCC) specifies that foundations and slabs for residential properties, being structural elements of a building, require that the assessment, design and certification of the design, specific to each site and structure, is carried out by a RPEQ Structural Engineer to assess, design and certify specific to each site / structure. This is where we navigate this for you!
Reactive clay soils are particularly troublesome, prone to expanding or contracting based on moisture levels. Excess moisture, including from nearby leaks (stormwater and/or sanitary), causes clay to swell, raising the slab/footings (called ‘HEAVE’). Conversely, less moisture, like from nearby trees (that take away the moisture in the soil), leads to soil shrinkage and bearing capacity thus settling the slab/footing (called ‘SUBSIDENCE’). Besides reactive soil, tress and leaks, there are also other issues that can affect the foundations of a building including: poorly compacted fill, under-designed footings, slope failure, nearby trees, broken or leaking plumbing pipes etc.
All of these issues can result in significant structural problems for a building’s foundations and slab. These are called ‘differential settlement’ movements which includes distortions (up, down or rotations) or deflections (change or deviation), and are far from desirable. Failure to address this can lead to significant structural issues.
The first indication that there is a foundation problem that the property owner might first see are generally cracks in exterior walls, cracks in gyprock in walls; separation around windows; gaps around doors, which thus becoming difficult to open and close.
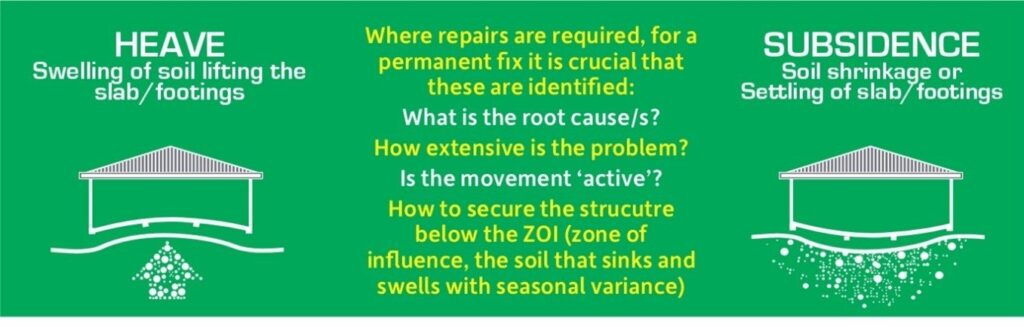
Section 2
Resin Injection used for Structural Foundation Problems:
Solution or Pitfall?
One method touted as a solution to such problems is resin or polyurethane injection ground engineering, often called ‘resin injection’ ‘resin grout injection’ ‘polyurethane injection’ ‘resin underpinning’, ‘underpinning’, ‘polyurethane underpinning’, ‘ground engineering’, ‘void filling’, ‘soil replacement’, ‘injection system’, ‘computer controlled grouting’. For the purpose of this article, we’ll use the global term ‘Resin Injection’.
Resin injection has since been widely used in Australia from around the ’90s as a ground strengthening exercise, particularly with reactive soils. However, we have observed that this method doesn’t always produce the desired results and has come into question in recent years, sparking debates over whether it’s a viable long-term solution or merely a temporary fix for larger underlying problems.
Resin injection can initially appear to alleviate the problem. It involves injecting resin or grout into the ground which fills up voids under the slab and expands, compressing the ground in an attempt to stabilise the soil and lift the ground underneath buildings and pavements that have shifted due to differential settlement (where one part of a structure’s foundation settles more, or faster, than the other). This method does not require excavation or the installation of additional structure elements (i.e. underpins to the footings or additional footings if required), making it a cheaper choice than traditional proven methods.
However, controversy surrounds this method, particularly among engineers. While resin injection has proven effective for mitigating liquefaction following earthquakes, its long-term reliability for homes with shallow foundations on reactive soils is uncertain.
And, a key here, for the public – resin injection to the soil is a soil treatment – it is not building works. Foundations are a structural element of a building, and works to the foundations including rectification works require building application and clients deserve the protection this offers them.
However, resin does not appear to require a building application. Despite organisations offering this method, it is not building works. Often organisations put on their materials and quotes that they have a builders licence, are part of Master Builders etc. However, that does not mean that the works are designed, engineered, or certified under the National Construction Code (NCC), nor have the building works protection of the QBCC Home Warranty Insurance. We have written a Consumer Education article on some questions to consider asking a resin provider when you are thinking of having foundation works done. It is crucial to understand your rights and what you are paying for before making any decision that you will be responsible for:
Due Diligence Consumer Questions for a Resin Provider
Section 3
Why Resin Injection is called Ground Engineering
When it comes to raising, and re-levelling a footing / slab there are a few different options to explore. Structural engineers often recommend conventional underpinning, which involves excavating around the foundations at intervals installing the underpins. This is a structural solution to a structural problem, and both the problem and solution are identified and designed by a REPQ Structural Engineer, who is required to certify the resolution.
Resin injection is a different process however and it offered as a soil treatment that can be delivered fast with minimal disruption and it requires no excavation or heavy machinery. However, with advancements in traditional underpinning, particularly screw pile underpinning, the time differences and disruptions are closing rapidly.
Where resin injection is useful is with underpinning historical and heritage buildings (see below ‘The original intention of resin injection – a short history’) These old buildings are often built on significantly shallow founded bluestone footings, instead of our modern slabs on ground, and sometimes impossible to use traditional underpinning methods. In some cases, resin injection is the only method that can provide the stability needed to preserve these important unstable historical buildings. However, it’s not without its drawbacks. Ongoing maintenance and repeat applications are factored into budgets. Resin injection used in other applications may not always address underlying issues and could worsen problems if not executed correctly.
So unless you’re buying an old church and considering resin injection, it isn’t always the best solution for remediation and improving the foundation soil below footings and can sometimes make the problem worse. In some cases, it has made little to no difference in floor levels and movements of the house. It’s essential to address underlying causes before proceeding with any ground engineering works. Moreover, differential movements of footings can cause significant damage if not properly managed.
Also, unlike Foundation Solutions who ascertain where services to the property are (sewer, plumbing, etc), resin injectors may not. The holes drilled in and around the home by resin injectors may infringe, damage or fill areas that are undesirable like plumbing pipes. These may not be known or identified at the time of application, but at a later date. This infringement of services by drill holes or resin cause considerable additional and expensive problems for owners, as you can see from the picture below where resin had been used for foundation repairs.
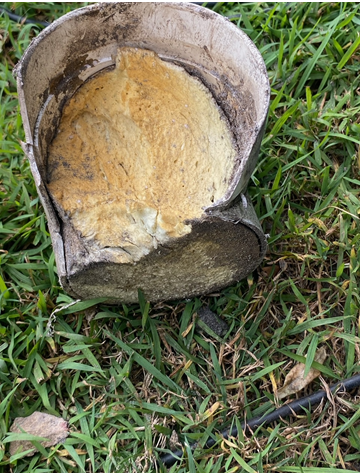
Section 4
Why we reject resin injection to repair foundation structural problems
Resin injection can at first appear a quick, cheap and easy way to fix the problem. However, we quickly identified 10 top reasons that there are, in our view, numerous pitfalls with this method.
From our experience in the industry, we have noted and identified the following problems from the use of resin injection to repair foundation issues: –
1. We have received numerous enquiries as a result from customers seeking alternative foundation works due to a failed resin injection; one main reason, is where their home has received little to no lift when that was the purpose of the works and what the customer thought they were paying for;
2. A RPEQ registered engineer has not conducted the site review and provided a comprehensive report to assess the foundations issues that warrant this approach;
3. Lack of detail in identifying the root cause/s, how extensive is the problem;
4. Lack of detail in addressing how to secure the structure below the ZOI (zone of influence – the soil that sinks and swells with season variance);
5. Lack of consistent building code compliance where works are carried out without registering the works with the QBCC to oversee licensing and regulation; dispute resolution; building codes and standards, home warranty insurance, compliance and enforcement and consumer protection to ensure safety, quality and reliability of works;
6. Lack of transparency in the cost to the client – we have observed where the final cost to the consumer has not been able to be accurately predicted (as it is the least quantifiable method) and blows out beyond initial estimates;
7. Lack of control in where the resin is injected – we have observed many sites where resin was found in service pipes, severely interfering with the functionality of the property; and with waffle pods that material fills up voids with the pod arrangement wasting material and your hard earned money;
8. The lack of accountability for works performed where we have observed that when a failure is identified they discovered there was no guarantee on the works performed (as only the product was guaranteed, that did not shrink, and the warranty was on the product only) and the additional cost to continue repair works had to be covered by the consumer – in effect paying twice to solve the problem;
9. Lack of transparency in the cost to the client – we have observed where the reporting to the client involves paying additional costs if they want the full report or if engineers are required that is at an additional cost;
10. The controversy surrounding this issue amongst Structural Engineers.
You may wish to read further regarding engaging Engineers in our article:
Consumer Education – Due Diligence Questions for Engineers
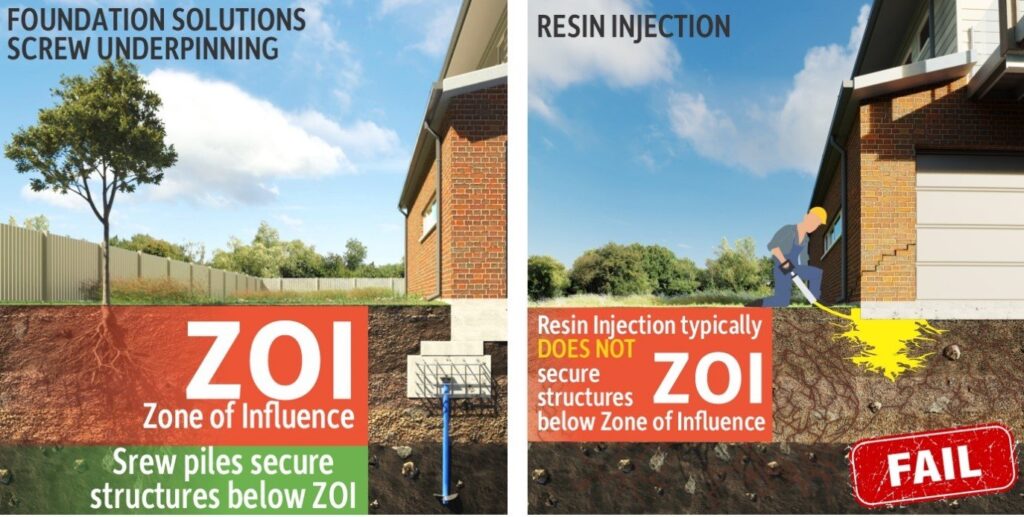
Because these pitfalls were too many in our observation, and we had heard far too many sad and heart breaking stories about resin failing and/or causing other problems, and not achieving the best result required for the home owner, we rejected the use of resin for subsidence issues in residential foundations with reactive clays.
As Foundation Solutions have the required skillset, licensing and qualifications to be able to be selected to use a superior method using Katana screw piles, we don’t use nor recommend that resin / polyurethane / grout be used for residential structural foundation repairs for reactive clay environments.
In our extensive experience, resin injection is not the permanent solution you need for peace of mind. It’s simple, if a foundation is compromised and it is determined by a qualified expert (a REPQ registered engineer) that it is a structural issue, it requires a structural solution. It is why we engage specialist experienced and independent RPEQ registered structural engineers who assess, plan and certify all underpinning work we undertake. We respect their findings and advice and they are bound by a strict code of ethics. All photos, contours, levels and reporting is given to the client without restriction for full transparency to the client.
It makes us truly sad for consumers when they find out their resin application has failed, the warranties they thought they could rely on had disappeared, or works were performed when not required. As mentioned previously the Building Standards have criteria where movement is normal and not a concern, and works are not required. A crack does not mean panic. If the correct levels are taken by an expert, the conditions assessed with an expert eye, and it is explained to consumers so they are aware of these and the building code requirements, then they can make an informed decision.
We have often had to rectify foundation remedy works that previously tried resin injection where these works failed completely or did not permanently fix the problem. We have observed clients in distress by the double handling, lost time and extra cost that these property owners incur because problems showed up later. Whilst it is a cheap option, you get what you pay for and you receive less. The distress and cost of rectification has often placed a burden on the buyer that has negatively impacted them both emotionally and financially, in our opinion, has been cruel to watch.
“I came across a lady, and she just recently purchased a property. It wasn’t disclosed to her that the property had some serious structural defects, and that it had resin injection underpinning done to it. Subsequent to that, they called us out, as the resin has not worked. The devastating thing for her was she comes from Victoria, where she said she believed there’s full disclosure around these issues, but it wasn’t the case for them in Queensland where a seller did not have to disclose issues or these types of works. We got a structural engineer out to have a look at it, and it needs structural underpinning at a cost of $80,000 which is a significant cost Had they known, they perhaps may have made a different decision, and it is now putting a severe financial bind as to what they do. And from what I know, in Queensland they don’t have any recourse about that. She was disturbed that the resin did not work and that they had no knowledge what had been done to their property prior to purchasing. Foundation matters can be a $6,000 cost or, in this case an $80,000 cost because the prior works did not work, and the problem has worsened. I hear these stories from consumers all the time, and I feel it’s important there is transparency around these issues, and to inform consumers when they are looking to purchase a property, what questions to ask.”
“It wasn’t disclosed to her that the property had some serious structural defects, and that it had resin injection underpinning done to it. Subsequent to that, they called us out, as the resin has not worked. ”
Section 5
Why we have rejected resin and have instead chosen
Screw Pile Underpinning using Katana Foundation’s Codemark Screws
Firstly, we did not want these calls – that the resin had failed, appeared in plumbing, or that the problem has not been rectified and continued.
We wanted a product and solution that we could guarantee a structural fix for a structural issue. One that can be delivered fast with minimal disruption, would address the entire range of problems in what is really a complex issue. We also wanted to be able to stand proudly in the market with industry leading guarantees, as we intended to be in the industry for the long term.
With considerable research, accreditation, credible and recognisable partnerships we have developed the proven ‘Wunderpinning’ method using CodeMark certified Katana Screw Piles. CodeMark Certification is a third-party building product certification scheme, administered by the Australian Building Codes Board (ABCB), designed to provide confidence and certainty to consumers and regulatory authorities that building codes have been met, through the issue of Certificates of Conformity:
https://katanafoundations.com.au/codemark
All of our works fall under QBCC legislation, are fully insured by QBCC and we follow all building code specifications, standards and best practices. This provides our clients with peace of mind and industry-leading guarantees that exceed the standards. We are proud to be on the ‘Subsidence Panel’ of selected providers that QBCC will use when foundation problems arise and it falls under their insurance provisions.
We are also aware foundations and footings are structural issues according to the National Construction Code (NCC). This means the correct model for assessing the problems, the rectification design for the problems identified, and certifying the works meet the code requires a structural engineer. This starts with identifying: (1) what is the root cause/s’; (2) how extensive is the problem; (3) is the movement active; (4) how to secure the structure below the ZOI (zone of influence – the soil that sinks and swells with season variance); and any works that may be required are inspected, assessed, designed, and construction is certified by an independent structural engineer.
Only once you have received a RPEQ structural engineer’s report after their site visit and remedial work is determined as necessary should you proceed. Unfortunately, we have observed times when unnecessary work was undertaken because it did not have the scrutiny of a RPEQ structural engineer, who is bound ethically to building standards and a code of ethics, watching the process. The next step is a structural design for the foundation remedy from a RPEQ structural engineer. This is implemented by a registered builder that specialises in foundation require to meet the building codes. These works are insured through the QBCC, you receive that precious and valuable “Certification” by the RPEQ structural engineer of the building works and the require warranties under the law are all yours. This is your best investment.
“Unfortunately, we have observed times when unnecessary work was undertaken because it did not have the scrutiny of a RPEQ structural engineer, who is bound ethically to building standards and a code of ethics, watching the process.”
No-one wants to pay money to resolve foundation issues. We understand. However, if the problem is there, your property’s worth is affected. It is easily remedied though and will add value to your property. Repairs using traditional underpinning are identifiable, quantifiable and certified solutions to the problem. It is in fact a valuable ‘home improvement’ which will ensure your property is both sound and safe – and you don’t waste your money.
On a side note – we have never had a claim lodged against us with the QBCC where we have undertaken works that have failed. Our solution is individually crafted and specifically designed specific to you, and one of the biggest investments of your life.
Section 6:
The original intention of resin injection – a short history:
In civil engineering, ‘grouting’ is the process of injecting pumpable materials (resin or the like) into a soil or rock formation to change its physical characteristics. This technique has been used since 1800, when it was first used to repair a sluice in Dieppe, France. Since then, it has been used to fix dams and other structures. In 1950, the process of compaction grouting was introduced. This involved using a zero-slump grout made of cement, sand and water to compress any weak materials in a foundation.
The idea of using resin for ground strengthening was originally introduced by a Scandinavian company to help address ground movement and subsidence. It is a homogenous mixture in two parts. When the resin is injected into the soil, it reacts, forming a rapidly expanding foam that seeps into any ground voids and fissures, filling gaps and lifting the structure, lifting settling issues without the need for digging.
After the Newcastle earthquakes in 1989 and the damage to the city’s iconic heritage building that dominated the landscape, Christ Church Cathedral, Newcastle City Council need to define a new standard for building works and repair of older buildings (which started years of argument among engineers and architects). Estimates and repair costs were substantial ranging between A$1.6 million and A$12.6 million, with an immediate priority to make the damaged structure safe for the public. After much argument, it was decided the primary aim of the structural design was to turn the building into a ductile building (a measure of how much a material can be deformed or elongated under stress before it fractures).
In the end, a combined system was chosen which used supporting timber frames and stainless steel combined with resin within the building, also in the roof space and inside the tower together with a ground anchor system to carry the load. The anchor system was used around the perimeter of the building, and consisted of stainless-steel end plates, intermediate plastic plates, and a fill of cementitious grout in a tubes of woven fabric, which controlled the grout being injected, with regular stations inserted into the brick. This process ensured the sock can be monitored. Remediation works continue on the Church, with constant appeals for funding.
Section 7
Is Resin Injection Really Underpinning?
In our opinion and experience, the term “underpinning” is often misused in the industry, frequently applied without involving a Structural Engineer as intended.
A research paper (funded by the resin industry) by the University of Newcastle stated that:
“foundation remediation techniques using polyurethane foams have only appeared in the last 25 years and a “deep lifting” process has been patented more recently (Canteri, 1998), which from a geotechnical perspective is at the border between underpinning and grouting”. Further, “When injecting the foam into a desiccated clay, it is observed that it can either propagate through existing cracks or it can create new fractures in the soil”.
It is of note that resin injection was not noted as ‘underpinning’.
Underpinning is the process of supporting or strengthening the foundation of an existing house. The foundation of a building according to the National Construction Code consist of the footings and slabs to existing buildings and extensions. The resin injection method, and the research paper, discuss how the foam does in fact bond with the soil, but it does not state nor claim, that it improves the foundations as defined by the code, let alone provide a permanent solution.
Underpinning of the footings of the property, particularly the method we employ, screw pile underpinning, allows a cost-effective reach to deeper depths securing the structure below the zone of influence, the soil layers that shrink and swell with seasonal influences. Other methods, including resin, do not secure at this level and are only a band aid solution.
Troy Williams, Technical Manager of BuildCert has advised:-
“The intent of the following is to provide clarity and a base level understanding of Queensland Legislation regarding underpinning work.
Queensland Legislation
In accordance with the Building Act 1975, underpinning (whether by vertical or lateral support), inclusive of incidental excavating or filling, is defined as ‘building work’.
To determine whether this type of ‘building work’ triggers a Development Approval for Building Work (Building Approval), refer Schedule 1 of the Building Regulation 2021.
Part 4(4)(2) of the Building Regulation 2021, in part, states the following, “The building work mentioned in schedule 1 must comply with the relevant provisions within the meaning of section 21(5) of the Act”, (e.g., Queensland Development Code, Building Code of Australia, Australian Standards).
Schedule 1(8)(1)(b) of the Building Regulation 2021, in part, states the following, “the building work— (ii) is for, or only affects, a minor structural component of the building.”
Definition of a minor structural component, in part, states the following, “(c) if the work is adding the structural component to the building—the addition does not pose a risk to the building’s general safety and structural integrity.”
So, what is underpinning work (whether by vertical or lateral support), and what are some typical forms of underpinning work?
In simple terms, underpinning could be identified as building work that involves an additional form of foundation/s installed beneath the ground of an existing building/structure to support and/or strengthen the building/structure.
Three main underpinning techniques/systems often performed in SEQ consist of, but not limited to,
a) Mass concrete underpinning,
b) Screw pile underpinning,
c) Grout/resin injection underpinning.
In conclusion, underpinning work is building work typically performed retrospectively to an existing building/structure to assist in reducing / eliminating the likelihood of further structural distress whilst renewing the ability of the existing building/structure to perform in a manner that does not further compromise the building’s general safety and structural integrity.
Therefore, this type of building work is widely considered building work that does pose a risk to the building’s general safety and structural integrity and consequently is considered assessable building work that requires a Development Approval for Building Work prior to the work being performed.
The Development Approval for Building Work process is a legislated process that ensures building work (underpinning work), conforms with relevant legislation, including but not limited to, the Building Code of Australia and Australian Standards.”
“Underpinning work is building work typically performed retrospectively to an existing building/structure to assist in reducing/eliminating the likelihood of further structural distress whilst renewing the ability of the existing building/structure to perform in a manner that does not further compromise the building’s general safety and structural integrity”
— Troy Williams, Technical Manager of BuildCert
The Australian National Construction Code specifies an engineer must be involved:
The National Construction Code of Australia sets out the standards for residential foundations where footings and slabs. They requirements sets out classifications of a site and the design of the footing systems for the slab, including size and placement of reinforcement, including shrinkage control and performance requirements. In civil engineering, it is important to know how the loading system and load path works in the structure. In any structure the load is applied on the slab which is transferred through beams and in turn these beams puts loads onto the column which are eventually transferred to the foundation. From here the loads ‘exit’ your structural system and transferred to the earth or soil beneath it. The foundation must rest on hard strata, and the assessment of the soil classification at the time is crucial. The design of the footings is based on a combination of several processes including:-
Soil Investigation:
Before the structural design of a foundation is done, the soil is investigated to know the soil characteristics, soil bearing capacity (SBC), the different layers of soil beneath the proposed structure, all of which information helps the engineer determine the type of foundation suited to the structure. This assessment is done prior to construction, and it is of note that soil conditions can change over time. Soil conditions are assessed under the code when the property is originally built on. As soil conditions change if there are been influences on the soil over time (water, trees etc), it necessary for the Engineer to take this into consideration, and there may be a need to reclassify the soil. It is with this expertise, that an qualified and experienced structural engineer will design what rectification works are required for the current classification of the soil conditions.
Structural Analysis and Design:
It is mandatory to perform a structural analysis of the proposed building, including various reactions, coefficient of friction of soil and concrete, shear forces, bending moment forces acting on the structural elements, in particular at the supports of a foundation design. A structural design process needs to be followed to design in response to the soil investigation report, and the structural analysis and requirements of the concrete footings needed to ensure the concrete structure is strong enough to support the forces being applied to it, to ensure the structure’s strength and safety.
Structural engineers can experiment with different sizes of the foundation, reinforcement arrangement and quantity required to find a result that makes a design more economical, without compromising the structure’s strength or safety. It is common to look at the governing result and determine why the structure is failing, then adjust some input (reinforcement, footing dimension) to improve the design.
You’ll note from the above, each step involves a Structural Engineer.
Section 8
We Are Here to Help – Ask Us:
In summary, before opting for resin injection, we recommend:-
1. Read our article on questions to ask both the company quoting you, and the engineer preparing the report (see the link in section 10 below);
2. Consult us to organise a a reputable RPEQ forensic structural engineer report. Each site presents unique challenges, and a thorough risk-vs-benefit analysis is necessary to determine the best course of action specific to that site and its structure.
The cost is not prohibitive for a proper RPEQ structural engineer’s report. It is a worthwhile investment for you and your home.
At Foundation Solutions we want to ensure your hard earned money works for you and your investment. It will also help you to clarify if you are being quoted by a slick cowboy in the industry.
Once the work is done, there’s no turning back, and guarantees can be meaningless, unless it is a warranty provided under the code. So, make an informed decision with expert guidance to avoid potential pitfalls.
Get in contact with us, to conduct a complimentary home checkup, need a second opinion on a foundation inspection or a Structural Engineers Report. We will organise everything for you and connect you with our Trusted Network.
Section 9
Obtain Another Opinion – Ask Us
There are a lot of questions to ask – we know. It can be a difficult and distressing process to navigate and understand. Especially when it involves one of most people’s biggest investment in life. Further, the small print and exclusions that can make the consumer liable or have shortfalls that do not protect them can be hard to detect.
Of course, we believe the best solution is to come to Foundation Solutions first. We are committed to providing solid education based on what the law states, what is needed to provide a correct and reliable solution and to back up our works with industry leading guarantees that do protect the consumer. The questions below above aim to give the consumer enough information to assess whether they can rely on the proposed solution.
We encourage consumer to consider Foundation Solutions for your project, particularly if the suggested approach involves using resin or concrete bored pier providers. We believe we have a superior product and solution and have a comprehensive understanding of where these other methods might fall short in delivering the desired results or guarantees.
If a consumer would like us to review the information they have received, we offer this as a complimentary service. We will highlight any areas of concern based on our experience and perspective. This offer is available to consumers who have not yet engaged another party for repair or rectification work and includes:
FREE REVIEW SERVICE:
Engineer Reports and Quotes
Resin Repair Reports and Quotes
Concrete Bored Pier Reports and Quotes
Underpinning Quotes
Please note that this is a complimentary service and does not constitute a contract between Foundation Solutions and the user.
SECTION 10
What does the law say?
In essence, the stability and reliability of your footings and slab (foundation) of your house and the guarantees and warranties for those works is determined by:-
1. Consumer laws and protections;
2. Soil classification;
3. The design of the foundation (depth and initial design) to suit those conditions; and
4. What has changed since the original design, and what is needed now;
These factors are all governed by legislation to protect consumers, including:-
A. Consumer Laws, Protections and Confusion in the Market
As part of consumer and fair trading laws, the ACCC regulates customer guarantees. Consumers have basic rights, known as consumer guarantees, and businesses must provide an automatic guarantee to consumers with any product they sell.
In addition, certain works on residential buildings, like foundation works, fall under the National Building Code, and in Queensland, application is required to be lodged with the Queensland Building & Construction Commission (QBCC) for these works. The QBCC advise that most residential building work (this includes foundation repairs) in Queensland valued at more than $3,300 (including materials, labour and GST) must have insurance cover under the Queensland Home Warranty Insurance Scheme to protect consumers. This specifically includes works that affect the structural integrity of the building. The construction works that don’t require home warranty insurance is driveways, paths, fences, air conditioning, hot water systems, security doors and grilles and landscaping.
A business may also offer additional warranties to the consumer for the works that they undertake.
There is confusion in the market about what guarantees and warranties are actually being offered in this industry. Often it is a warranty about the product’s quality, not a warranty about the works being undertaken, and there are instances where no QBCC application is lodged and no insurance organised for, or paid, to protect the consumer.
With foundation issues, consumers should seek to understand both the product guarantee and the works warranty and request copies of all documents, including the application to QBCC and the insurance coverage document.
For example, at Foundation Solutions we use Katana Screw Piles which are CodeMark certified to confirm to the National Construction Code requirements have been met. We lodge the required application with the Private Certifier for Building Approval and also take out the necessary QBCC insurance so the consumer is protected as required by law. We lodge the required Form 15 compliance certificate together with a Form 12 Engineer Inspection and a Form 43 for Termite Spray to Underpinning Areas. We provide our clients with copies of these for the future use and protection. We then provide a warranty for 8 years to our clients that exceeds the industry requirements. Note, we have never had an installation fail nor any claim against us.
You can read more at:
https://www.accc.gov.au/consumers/buying-products
https://www.qbcc.qld.gov.au/running-business/home-warranty-insurance-obligations/what-work-requires-insurance
B. Australian Standards:
The reactivity of the soils beneath a property will play a part in how our homes behave over the life of the structure. This in turn plays an important role in the extent of the damage and the method of underpinning best suited to support, arrest the damage and lift or stabilise a residential home building. Soils are identified by Site Classification in accordance with ‘Australian Standards AS 2870/2011, Residential Slabs & Footings’. These standards show when it is time to take action.
At Foundation Solutions: We only do works that are required, as not all cracks need remedy.
C. The PE Act (Professional Engineers Act):
Engineering services are governed by law, The PE Act. The main objectives of the act are “to protect the public by ensuring professional engineering services are provided by a registered professional engineer in a professional and competent way, to maintain public confidence in the standard of services provided by a registered professional engineers; and to uphold the standards of practice of a registered professional engineer.
The PE Act in Queensland states that a ‘Professional Engineering Service’ is defined as: “An engineering service that requires or is based on the application of engineering principles and data to a design or to a construction, production, operation, or maintenance activity relating to engineering” (see page 113 of the PE Act).
If you are engaging an engineer, ensure they are registered with the Board of Professional Engineers, who assess candidates as to their qualification and competency and issue a letter of assessment and fitness to practice. You can search to see if the person you are working with is a professional engineer at:
https://portal.bpeq.qld.gov.au/BPEQPortal/RPEQ_Directory
At Foundation Solutions: We only use RPEQ registered Engineers that specialise in foundation movement and assessments for your protection! These reports are tailored for you and your home, are transparent and comprehensive, and designed to be able to be relied on to keep you and your property secure and safe.
SECTION 11
Consider the small print in a report or quote:
A qualified RPEQ Engineer adheres to a strict code of ethics and performance guidelines, ensuring their reports are reliable, comprehensive, and can be used by others, such as for designing rectification works.
It is important to be aware of the limited scope of reports, quotes, services, and guarantees or warranties. Consumers are encouraged to carefully review the small print to ensure that the information provided is reliable, comprehensive, and compliant with building codes. Be mindful that some providers will ask for additional costs for the consumer to obtain full disclosure reports.
SECTION 12
FURTHER INFORMATION, RESOURSES AND ARTICLES:
To be fully informed on the subject of foundation issues and the facts you need to gather to make an informed choice of provider and resolution, you may wish to also read:-
1. Consumer Education: Due Diligence Questions For Resin Providers: Critical Questions Consumers should ask Resin Providers before engaging them.
2. Consumer Education: Due Diligence Questions For Engineers: Critical Questions Consumers should ask Engineers before engaging them.
3. Foundation /solutions Screw Pile Method -v- Concrete bord piers.
4. Buyer Beware: New property Law in Qld – Seller Disclosures
5. Top 8 Reasons to use Screw Pile Underpinning
6 Cracks in Walls> Here’s how to determine if they are serious (and what to do about them): Superficial, Serious or Structural.
Disclaimer: The content on this blog/document is intended only to provide a general summary of information of interest – namely to get consumers thinking about what questions they ought to consider asking prior to engaging an entity to provide foundation advice/services.
It is not intended by the writer to be comprehensive nor does it constitute any sort of advice (building/legal or otherwise).
While Foundation Solutions endeavours to ensure that the content of this blog/document is and remains current, we do not guarantee its accuracy.
This is particularly the case whereby the building industry by its very nature is prone to changes in procedure and standards.
Further, this information is general in nature and does not take into account your personal circumstances.
No two structural foundation matters are the same and each matter needs to be reviewed before a proposal and your avenues available can be given to you for consideration.
You should seek professional advice before acting or relying on any of the content of this blog/document or engaging an entity for foundation services.
To be clear, your use of any information contained in this blog/document is not intended to create nor does it create a customer-client or fiduciary relation between Foundation Solutions and yourself.